Suivez-nous sur
Contactez-nous | Téléchargez l'édition 2021/2022 | ©Atlas Copco AB
result
Search
UN MAGAZINE ANNUEL DU GROUPE ATLAS COPCO
Sustainable technologies
Markets
Smart manufacturing
Our culture
Service and Consulting
Energy efficiency
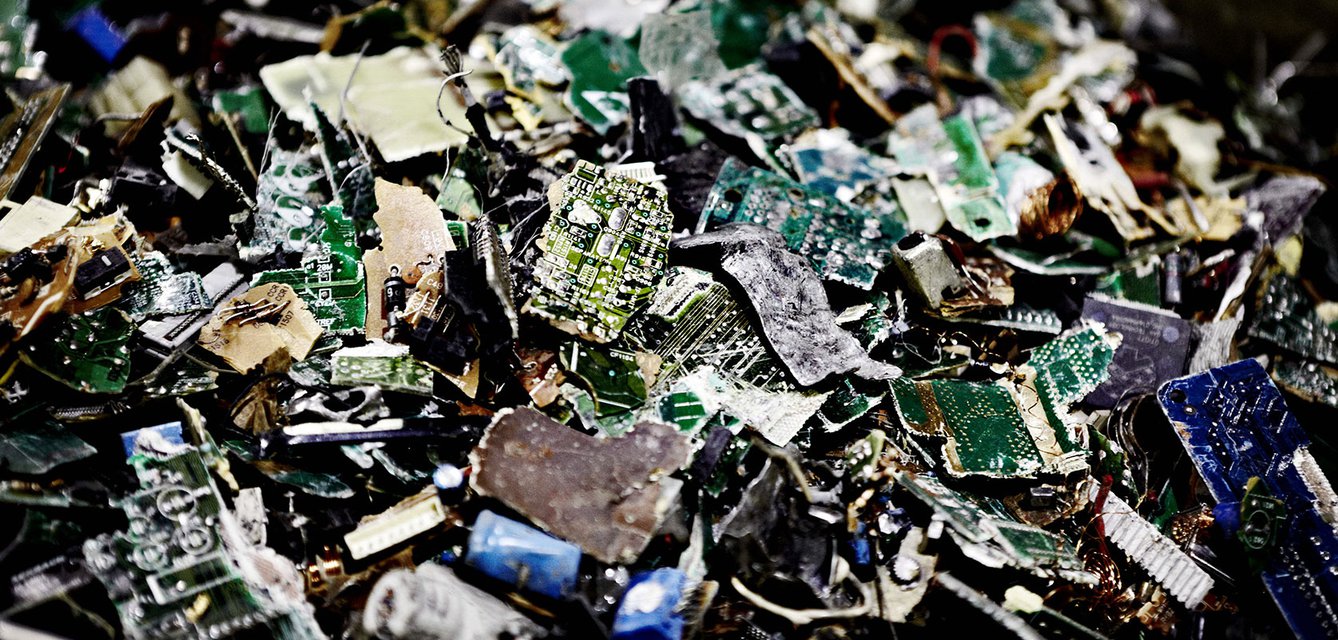
Acteur de l 'économie circulaire
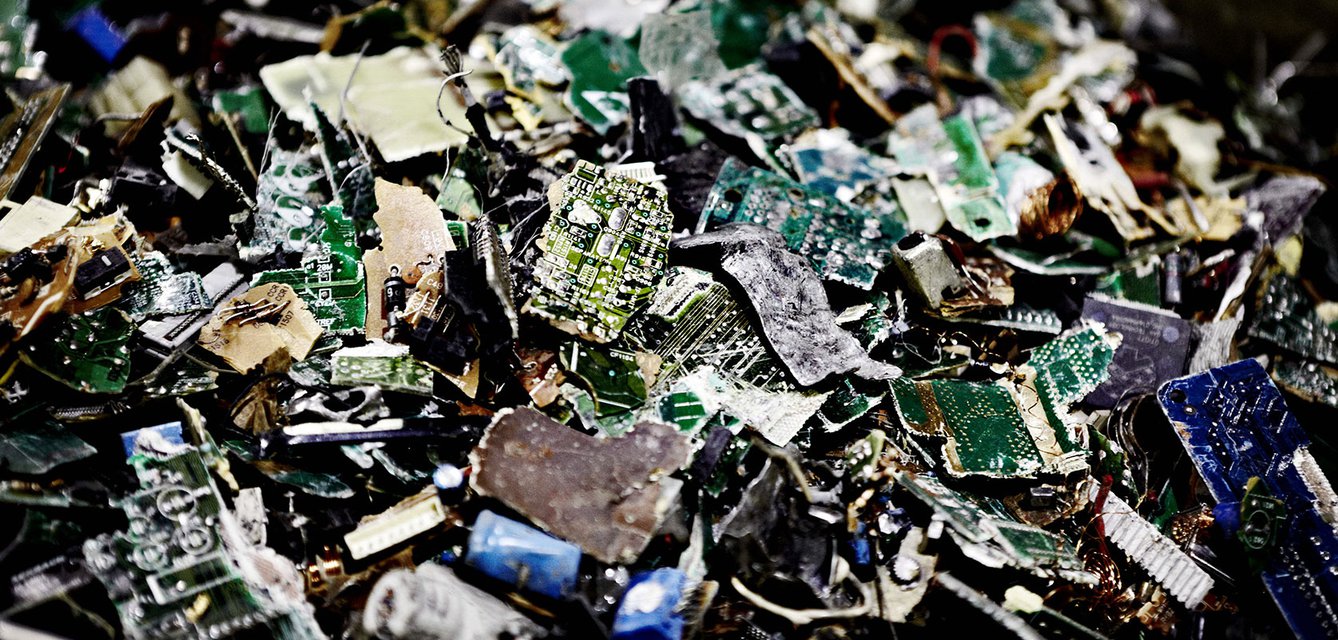
Saviez-vous que votre téléphone portable est une véritable mine d'or ? Boliden Rönnskär est l'une des plus importantes fonderies mondiales de récupération des métaux des dispositifs électroniques en fin de vie. Elle transforme les cartes de circuits imprimés en métal pur réutilisable dans de nouveaux produits. Bien que ce processus soit énergivore, la fonderie a réussi, avec l'aide d'Atlas Copco, à réduire sa consommation d'énergie de plus d'un million de kWh par an.
Contrairement à de nombreux autres matériaux, les métaux peuvent être réutilisés à plusieurs reprises sans perte significative de qualité. Boliden Rönnskär, située près de Skellefteå, dans le nord de la Suède, est l'un des principaux acteurs mondiaux du recyclage des métaux électroniques, tels que les téléphones portables et les cartes de circuits imprimés, et est un élément clé de l'économie circulaire.
Créée en 1930 pour transformer le minerai extrait des mines voisines en métal pur (comme le cuivre, l'argent et l'or), Boliden Rönnskär est aujourd'hui l'une des plus grandes et efficaces fonderies d'Europe. La plupart des processus de la fonderie nécessitent de grandes quantités d'air comprimé, ce qui implique des exigences élevées en matière d'efficacité énergétique et de sécurité opérationnelle des compresseurs.
En 2014, la fonderie a remplacé plusieurs vieux compresseurs par des modèles à entraînement à vitesse variable (VSD) plus économes en énergie. Pour avoir une idée précise du besoin en air comprimé des différentes sections de la production, Boliden Rönnskär a réalisé un audit énergétique (AIRScan) en collaboration avec Atlas Copco. Onze points de mesure de la compression et du débit distincts ont été installés à certains endroits du circuit d'air comprimé. Les mesures ont été réalisées pendant deux semaines alors que la fonderie était entièrement opérationnelle.
Les résultats ayant été analysé par des consultants spécialisés dans le domaine de l'énergie d'Atlas Copco, ont démontré que l'installation d'air comprimé existante était très économe en énergie, avec des chiffres bien en dessous de ceux préconisés par les directives de la Swedish Energy Agency, mais l'équipe en charge de l'air comprimé avait tout à fait raison. En investissant dans des compresseurs à entraînement à vitesse variable VSD et dans un système d'entraînement central, la fonderie a pu réduire sa consommation d'énergie de 850000 kWh par an dans un premier temps. En tenant compte des exigences de débit, de la compression et de la surface au sol disponible, Atlas Copco a présenté une proposition comprenant deux compresseurs VSD modèle ZR500VSD, qui venaient remplacer trois anciennes machines à vitesse fixe.
Suite à l'installation des nouveaux compresseurs et du système d'entraînement ES360, Boliden Rönnskär a mandaté Atlas Copco pour effectuer une mesure de suivi. Cette mesure a confirmé l'efficacité de la réduction de la consommation d'énergie, permettant ainsi à l'entreprise non seulement de réaliser des économies, mais aussi de réduire son empreinte environnementale de 11 tonnes de dioxyde de carbone équivalent par an. Les économies totales incluent également une diminution significative des coûts d'entretien.
La fonderie a depuis longtemps fait de l'environnement et du développement durable une priorité, ce qui l'a amenée à investir constamment dans des améliorations technologiques. En 2022, une vieille machine à vitesse fixe a été remplacée par un compresseur à vis sans huile modèle ZR750. Cette substitution a généré des économies d'énergie supplémentaires d'environ 200 000 kWh par an et réduit considérablement les coûts d'entretien à l'avenir. Boliden Rönnskär prévoit de remplacer l'ensemble de ses machines d'ici deux ou trois ans, ce qui devrait permettre d'économiser plus de 1 million de kWh par an, comparativement à la situation antérieure au premier audit énergétique en 2014.
* Le calcul de l'équivalence en dioxyde de carbone est basé sur une hypothèse d'émissions de 13 g d'équivalents CO2 par kWh.
Photo credit: Boliden AB
Articles suggérés